Albert Manero wins Fulbright Fellowship to conduct doctoral research at DLR in Cologne, Germany
Laboratory
In-situ characterization of high temperature materials
Raghavan’s group is experienced with capturing high resolution in-situ material response under conditions of large thermal gradients and/or mechanical loads. These tests are conducted in conjunction with transmission X-ray diffraction using the synchrotron source of Argonne National Laboratory [1]. Materials are probed under in-situ conditions to reveal crystal phase composition, transformation and strains with high energies of typically 70-90 keV (Fig 1). These test capabilities allow the team to reproduce and capture quantitative data on material behavior under extreme environments associated with engine and hypersonic operation. Multilayered high temperature materials can be studied to understand the effect of operational conditions on interfaces and strain variations with loads and temperatures. The results help to identify the critical stages and parameters affecting strain evolution in layered materials with goals of contributing towards improving reusability in extreme environments.
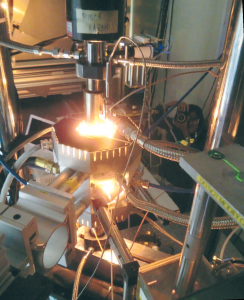
Fig 1: In-situ instrumentation developed at UCF in conjunction with synchrotron testing at Argonne [1]

Fig 2: Measurement techniques for the capture of diffraction data at the synchrotron in extreme environments. [2]
In addition, the novel measurement techniques [2] have been developed to capture coating behavior at the microscale resolution, studying oxidation and materials degradation in real time (Fig 2).
Phosphor thermometry using rare-earth doped sensing coatings for gradient testing
Our group studies the use of rare-earth doped sensing coatings to measures temperatures through luminescence lifetime decay or spectral intensity ratio emitted from the embedded sensor coating (typically rare-earth or transition metals). Luminescence lifetime decay decreases with temperature and intensity either remain constant until reaching luminescence quenching temperature from which it starts decreasing rapidly or increases in the case of thermal filling of the energy level. Coupled with models of luminescence lifetime decay in layered material systems, these sensing coatings provide us temperatures at various thicknesses of a thin coating with good accuracy. We have developed a custom Phosphor Thermometry system (Figure 4) specifically being able to capture simultaneously multiple luminescence decays through the decomposition of the spectrum using dichroic filters and the acquisition of distinct wavelength using photomultiplier tubes (PMTs) providing a range of temperatures that can be sensed through luminescence lifetime decay. The measurements can be modified to produce information on delamination captured by changes in reflectivity in these areas. [3,4,5].
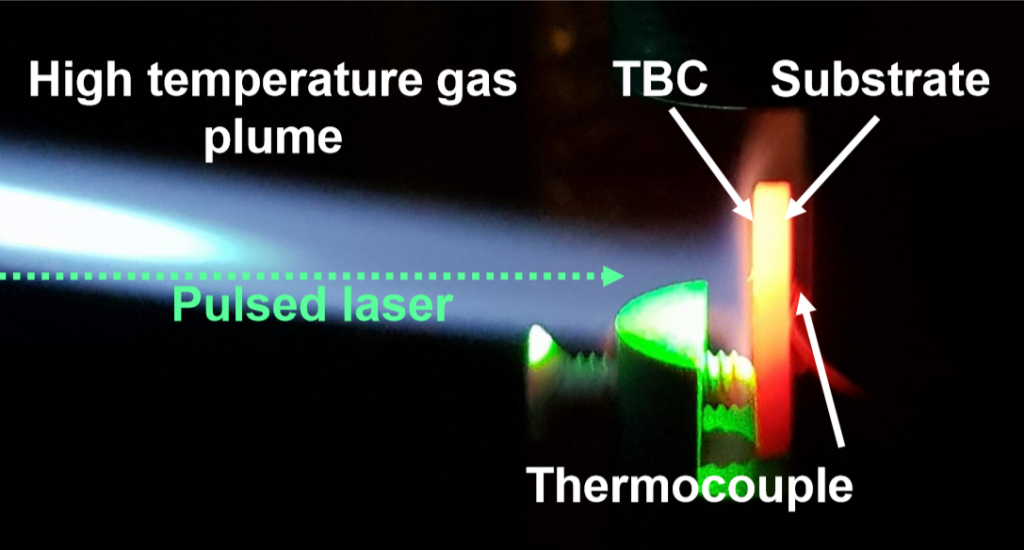
Fig 3: High heat flux testing with phosphor thermometry measurements for temperature sensing. [4]
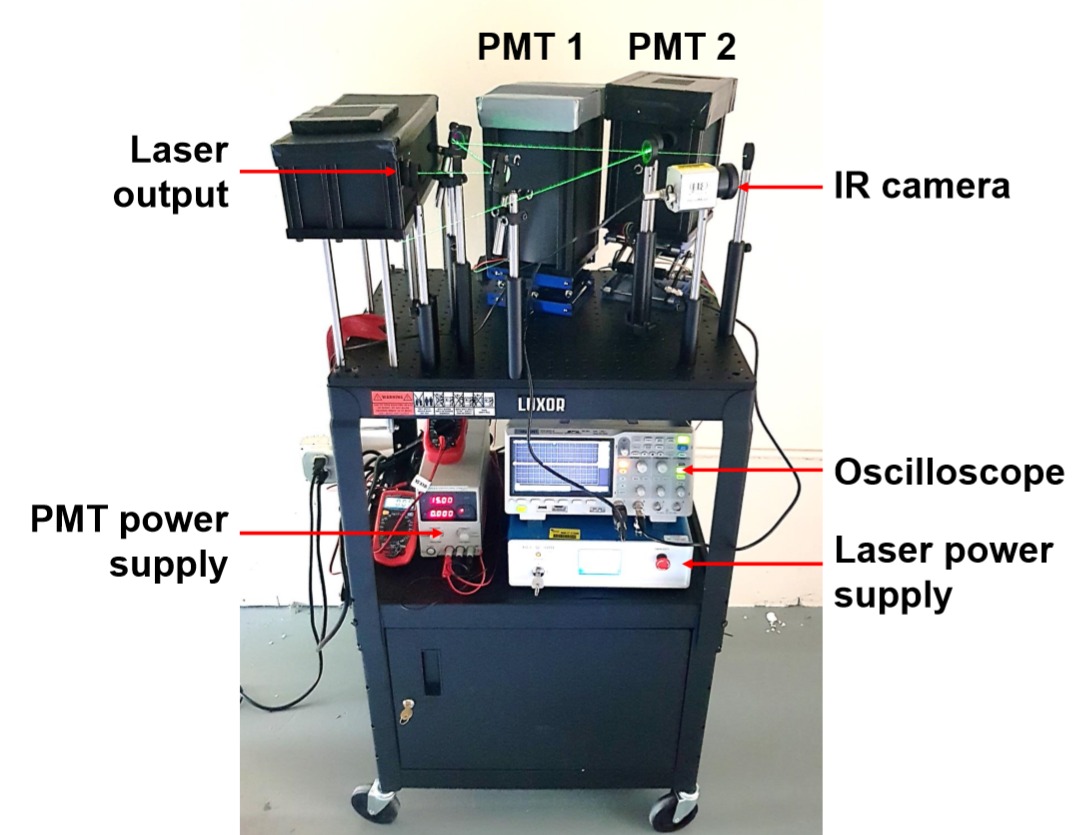
Fig4: PTS Schematic [5].
Spectroscopy and optical methods combined with thermal/mechanical loads:
We use a Raman microprobe system (Figure 5), which includes a Renishaw Raman RM-1000 spectrometer with a 532 nm laser source and CCD. The system is capable of performing standard microprobe-based analysis with objective magnifications of 5x to 50x for micron-level studies [6,7].
The portable photoluminescence piezospectroscopy (PLPS) system (Figure 6) is capable of taking spectroscopic measurements outside of the microprobe set up [3]. It allows for non-invasive and non-destructive stress detection. This system consists of a spectrograph, CCD, 532 nm variable power laser, and a fiber optic probe that is placed on an x-y-z stage to enable focusing on samples during loading. Key capabilities include automated stress mapping of samples based on Raman/photoluminescence peak positions. Samples are loaded, either in tension or compression, on an electromechanical testing system (Figure 7), which is capable of applying up to 50 kN of load. A hydraulic load frame (Figure 8) is also used and capable of reaching higher loads than traditional MTS systems (up to 100 kN).
Spectroscopy has been applied to studies that involve high temperature effects on aerospace materials and structures. Experiments were performed using IR chamber heaters. The former of the two heaters can reach up to 1300°C, while the latter can reach up to 1600°C. In addition, access opening holes allow mechanical loads while combining synchrotron XRD and optical measurement methods [1,8,9,10,11,12].
High-temperature digital image correlation (DIC) is also one of the options available in our lab (Figure 9) [13].
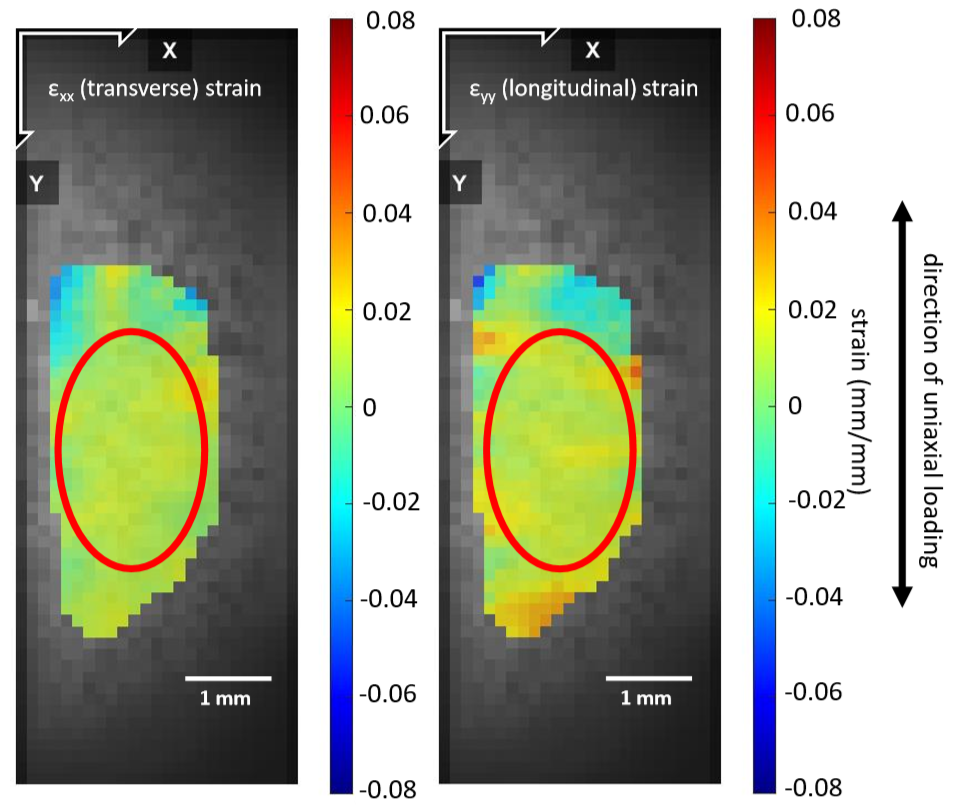
Fig. 9 High-temperature DIC used at the synchrotron beamline to study the thermomechanical behavior of Inconel 718.
The Thermal Mechanical Spectroscopic Laboratory:
The TMSL is a facility where high temperature experimentation, Raman spectroscopy, and mechanical experimentation are done. The facility contains a Hydraulic Material Testing System, shown in Figure 10, where mechanical loading testing such as tensile and compression testing is accomplished. Experimentation involving high temperature ceramics and materials is achieved by this system for space and hypersonic applications. A Renishaw Raman Microprobe System, as shown in Figure 11, is also available which allows for characterization of various thermal barrier coatings for the mitigation of CMAS infiltration.
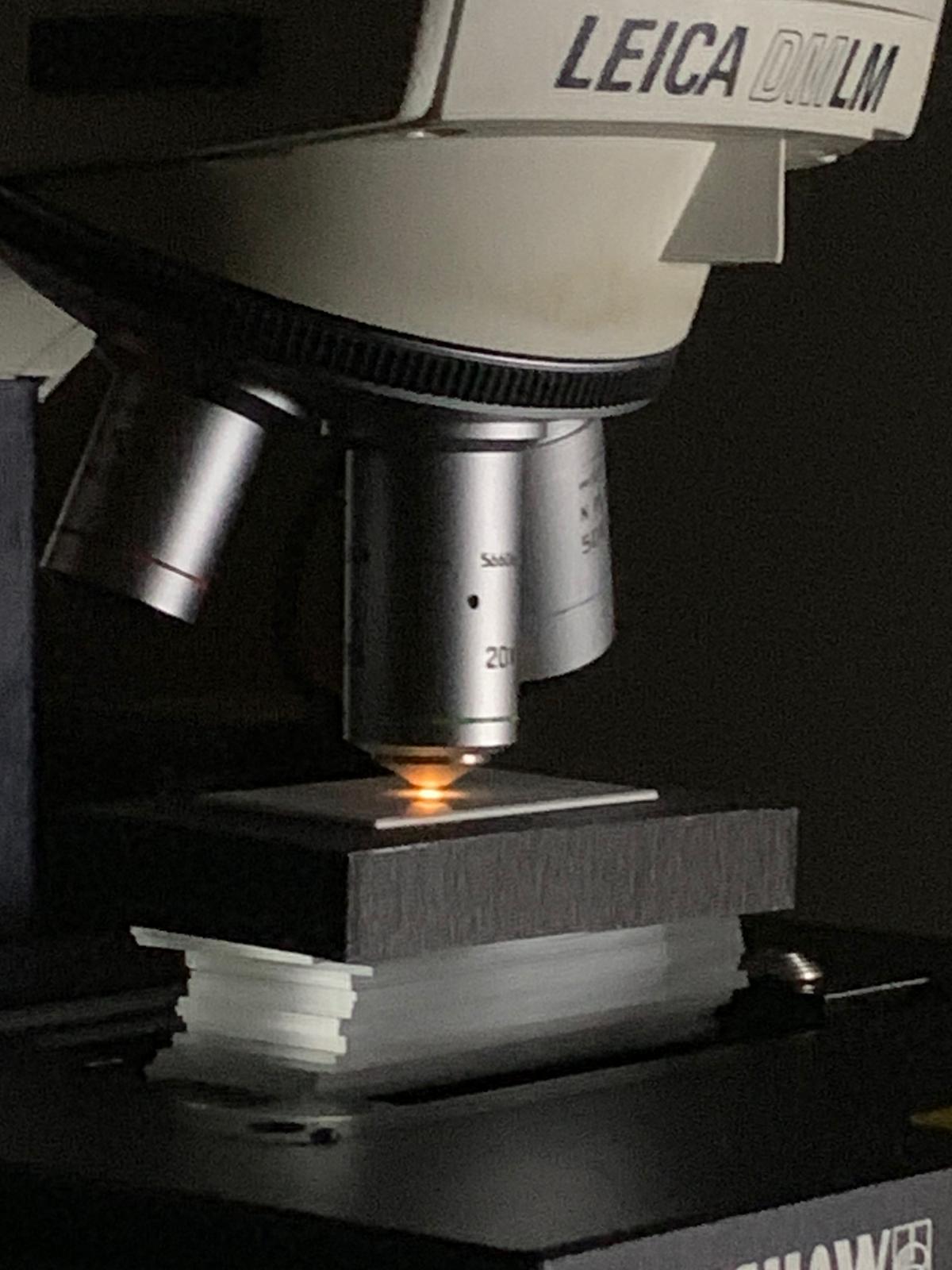
Fig 11. Renishaw Raman Microprobe System
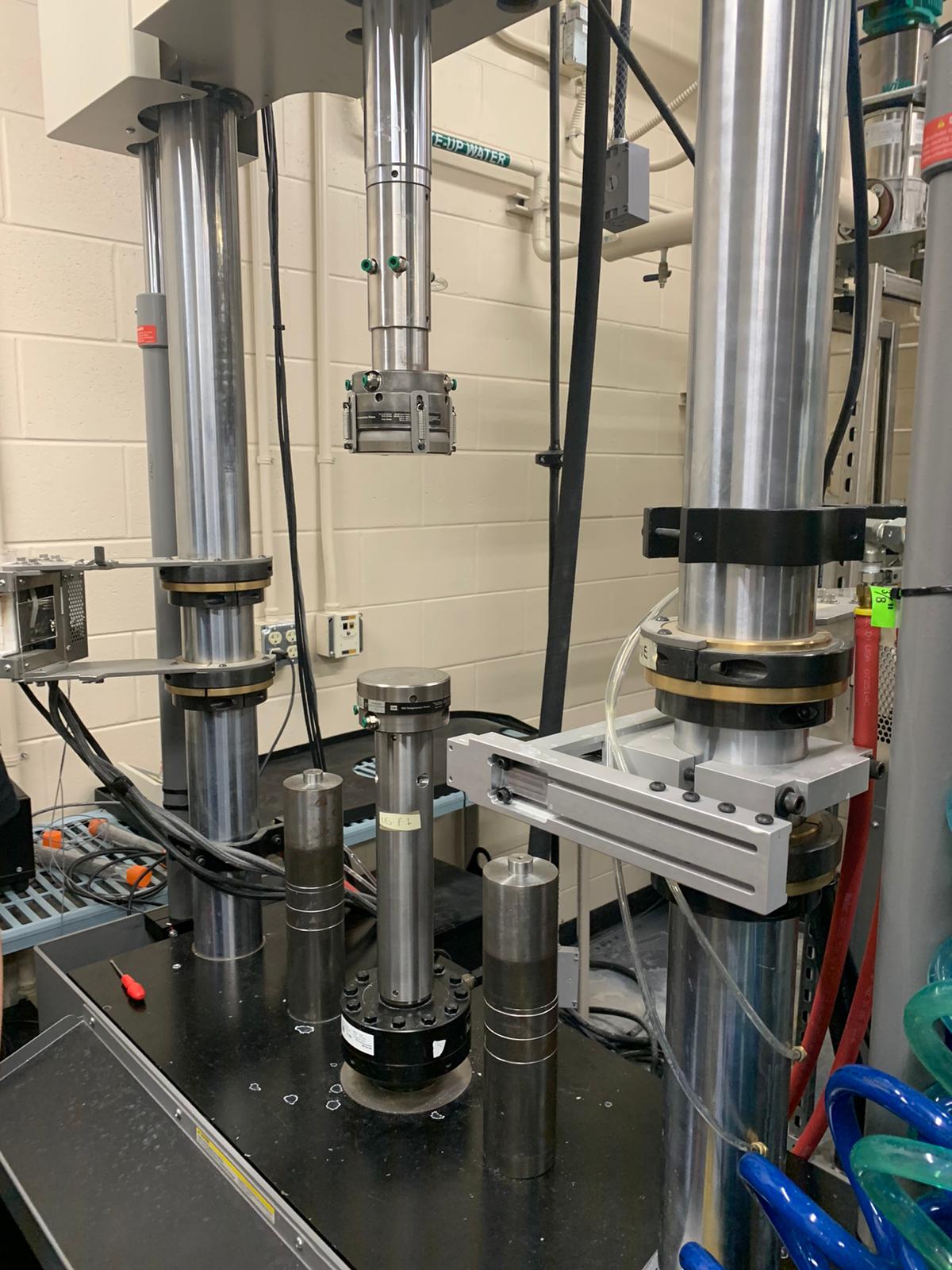
Fig 10. 810 Hydraulic Material Test System
References
- Kevin Knipe, et al. “Strain response of thermal barrier coatings captured under extreme engine environments through synchrotron X-ray diffraction.” Nature communications 5.1 (2014): 1-7.
- Albert Manero, et al. “Capturing the competing influence of thermal and mechanical loads on the strain of turbine blade coatings via high energy X-rays.” Coatings 8.9 (2018): 320.
- Quentin Fouliard, et al. “Modeling luminescence behavior for phosphor thermometry applied to doped thermal barrier coating configurations.” Applied optics 58.13 (2019): D68-D75.
- Quentin Fouliard, Ranajay Ghosh, and Seetha Raghavan. “Doped 8% Yttria Stabilized Zirconia for Temperature Measurements on Thermal Barrier Coatings using Phosphor Thermometry.” AIAA Scitech 2020 Forum. 2020.
- Quentin Fouliard, Johnathan Hernandez, Bauke Heeg, Ranajay Ghosh, Seetha Raghavan, “Phosphor Thermometry Instrumentation for Synchronized Acquisition of Luminescence Lifetime Decay on Thermal Barrier Coatings”, Measurement Science and Technology, 2020
- Gregory Freihofer, et al. “Ex-situ Raman spectroscopy to optimize the manufacturing process for a structural MWNT nanocomposite.” International Journal of Smart and Nano Materials 3.4 (2012): 309-320.
- Gregory Freihofer, et al. “Optical stress probe: in-situ stress mapping with Raman and Photo-stimulated luminescence spectroscopy.” Journal of Instrumentation 5.12 (2010): P12003.
- Sanna Siddiqui, et al. “Synchrotron X-ray measurement techniques for thermal barrier coated cylindrical samples under thermal gradients.” Review of Scientific Instruments 84.8 (2013): 083904.
- Albert Manero II, et al. “Piezospectroscopic evaluation and damage identification for thermal barrier coatings subjected to simulated engine environments.” Surface and Coatings Technology 323 (2017): 30-38.
- Selimov, Alex P., et al. “Characterization of hybrid carbon fiber composites using photoluminescence spectroscopy.” 58th AIAA/ASCE/AHS/ASC Structures, Structural Dynamics, and Materials Conference. 2017.
- Fouliard, Quentin, Ranajay Ghosh, and Seetha Raghavan. “Quantifying thermal barrier coating delamination through luminescence modeling.” Surface and Coatings Technology 399 (2020): 126153.
- Fouliard, Quentin P., Ranajay Ghosh, and Seetha Raghavan. “Delamination of Electron-Beam Physical-Vapor Deposition Thermal Barrier Coatings using Luminescent Layers.” AIAA Scitech 2021 Forum. 2021.
- Linda Rossmann, et al. “Method for conducting in situ high temperature DIC with simultaneous synchrotron measurements under thermomechanical load.” 2018 AIAA/ASCE/AHS/ASC Structures, Structural Dynamics, and Materials Conference. 2018.